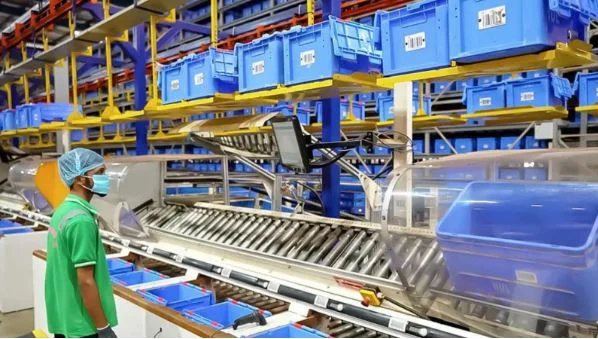
Thetechnotrick : Efficient warehouse order picking is the backbone of a smooth supply chain. Businesses that master this process increase productivity, minimize errors, and enhance customer satisfaction.
Every second counts in a warehouse. A well-structured order-picking system ensures that products move swiftly from storage to shipment, reducing operational costs and improving efficiency. This guide explores proven strategies, expert tips, and the latest technologies that optimize order picking.
Related:-
How a Well-Stocked Building Material Store Can Save You Time and Money
The Benefits of Hiring a Residential Architect in Denver, CO: Homeowner’s Guide
Understanding Order Picking in Warehouses
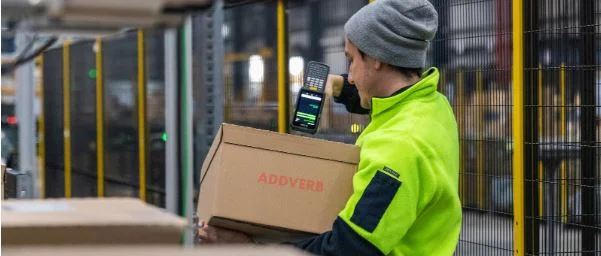
Order picking is the process of retrieving products from storage locations to fulfill customer orders. It accounts for nearly 55% of total warehouse operating costs, making it a crucial focus for improvement.
Types of Warehouse Order Picking Methods
🔹 Single Order Picking – One order at a time, ideal for small warehouses.
🔹 Batch Picking – Picking multiple orders at once, reducing travel time.
🔹 Zone Picking – Dividing the warehouse into sections, with workers assigned specific zones.
🔹 Wave Picking – A combination of batch and zone picking for maximum efficiency.
🔹 Pick-to-Light & Voice Picking – Technology-driven methods that reduce errors and speed up the process.
Optimizing Warehouse Layout for Efficient Picking
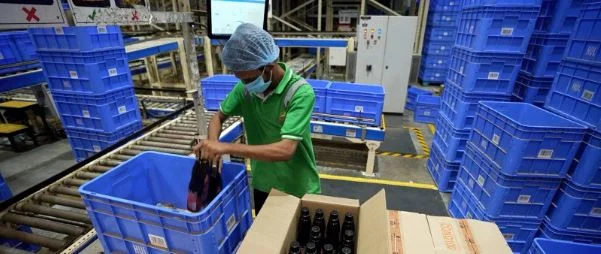
The layout of a warehouse impacts order-picking speed. A poorly designed warehouse leads to longer picking times, bottlenecks, and increased labor costs.
Key Warehouse Layout Strategies
✅ ABC Analysis for Storage Placement – Fast-moving items (A) should be stored at easily accessible locations, while slower-moving items (C) can be placed further away.
✅ Minimizing Travel Distance – Storing frequently picked products near packing stations.
✅ Implementing Pick Paths – Designing logical routes to avoid unnecessary backtracking.
✅ Reducing Aisle Congestion – Wide, organized aisles prevent delays and accidents.
An efficient warehouse layout saves time, reduces labor costs, and enhances overall productivity.
Technology-Driven Order Picking Solutions
Modern warehouses use technology to streamline picking, reduce human error, and increase efficiency.
1. Barcode Scanners & RFID Technology
Workers scan barcodes or RFID tags to confirm item selection, eliminating manual entry errors.
2. Warehouse Management Systems (WMS)
A WMS automates order allocation, tracks inventory, and optimizes picking routes.
3. Pick-to-Light & Voice Picking
🔹 Pick-to-Light – LED displays guide workers to the correct items.
🔹 Voice Picking – Workers receive audio instructions, keeping hands free for picking.
4. Automated Guided Vehicles (AGVs) & Robots
AGVs transport goods to workers, reducing walking time. Robots like Amazon’s Kiva Systems automate item retrieval, improving speed and accuracy.
Investing in advanced picking technology leads to faster fulfillment times and increased accuracy.
Best Practices for Faster and More Accurate Order Picking
A high-performing warehouse requires a well-trained workforce, strategic planning, and optimized workflows.
1. Training and Performance Monitoring
Workers should receive regular training on picking techniques, safety protocols, and technology usage. Performance metrics such as pick rate and accuracy help identify areas for improvement.
2. Implementing Batch and Wave Picking
Combining batch and wave picking reduces unnecessary movement and maximizes efficiency. This is particularly useful for high-volume warehouses handling thousands of orders daily.
3. Reducing Picking Errors
Errors cause delays, returns, and customer dissatisfaction. Strategies to minimize mistakes include:
✅ Standardized labeling and barcoding
✅ Automated verification systems
✅ Clear signage and item placement
✅ Regular audits and quality checks
4. Maintaining an Organized and Clean Warehouse
A cluttered warehouse slows down order picking. Organizing inventory, keeping aisles clear, and maintaining cleanliness improve workflow efficiency.
Overcoming Common Warehouse Order Picking Challenges
1. Labor Shortages and High Turnover
Warehousing jobs are physically demanding. High turnover disrupts productivity. Solutions include:
✔ Competitive wages and benefits to retain employees.
✔ Automation to reduce dependence on manual labor.
✔ Ongoing training to improve worker efficiency.
2. Seasonal Order Fluctuations
Demand spikes during holidays or special sales events lead to order fulfillment bottlenecks. Preparing for peak seasons involves:
✔ Temporary staffing solutions for increased workload.
✔ Stocking up on high-demand items in advance.
✔ Optimizing shift schedules for maximum efficiency.
3. Inventory Inaccuracies
Poor inventory management disrupts order picking. Using RFID, barcoding, and real-time tracking ensures accurate stock levels.
FAQs:
Q1: What is the most efficient order-picking method?
A: The best method depends on warehouse size and order volume. Batch picking is efficient for small orders, while zone picking suits large warehouses with high product diversity.
Q2: How can warehouses reduce order picking time?
A: Warehouses can minimize travel distance, use technology like pick-to-light, optimize layouts, and implement batch picking strategies to speed up order fulfillment.
Q3: How does automation improve order picking?
A: Automation reduces human error, speeds up retrieval, and minimizes manual labor, leading to higher efficiency and cost savings.
Q4: What are common order-picking mistakes?
A: Mistakes include picking the wrong items, poor warehouse organization, lack of training, and outdated inventory systems. Regular audits and automation help prevent errors.
Q5: What is the role of AI in warehouse order picking?
A: AI optimizes picking routes, predicts demand fluctuations, and enhances warehouse automation to improve overall efficiency.
Conclusion:
A well-optimized order picking system transforms warehouse operations, reducing costs and improving order fulfillment speed. Businesses that adopt advanced picking strategies, automation, and proper training achieve higher accuracy and customer satisfaction.
Warehouses must constantly analyze performance, adopt emerging technologies, and refine workflows to stay competitive in the fast-moving supply chain industry. Investing in efficiency today guarantees long-term success and profitability.
By following these proven warehouse order picking secrets, businesses can maximize efficiency, minimize errors, and streamline operations for a stronger supply chain.